Welding on MRT projects has become an essential skill in today's rapidly evolving infrastructure landscape. Whether you're working on constructing new lines or maintaining existing ones, understanding the intricacies of MRT welding can make or break your project's success. But let me tell you, it's not just about joining two pieces of metal together. It's about precision, safety, and ensuring that every weld meets the highest standards possible.
Imagine this: you're standing on a bustling MRT platform, watching trains glide smoothly past each other with millimeter-perfect accuracy. Behind the scenes, there's an entire team of skilled welders who've worked tirelessly to ensure those tracks are seamless and secure. The world of MRT welding is fascinating, yet often overlooked. But trust me, without it, our public transportation systems would grind to a halt.
Now, I know what you're thinking – "Isn't welding just welding?" Well, not exactly. MRT welding involves specialized techniques, materials, and processes that go beyond your average construction job. From understanding the types of welds used in rail systems to mastering the latest technologies, there's so much more to learn than meets the eye. So, buckle up because we're about to dive deep into everything you need to know about MRT welding!
Here's the thing though – this isn't just any ordinary guide. We've packed this article with insider tips, expert advice, and real-world examples to help you become a pro at MRT welding. And hey, if you're already a seasoned professional, maybe you'll pick up a trick or two along the way. Let's get started, shall we?
Table of Contents
- What is MRT Welding?
- Importance of MRT Welding
- Types of MRT Welding Techniques
- Materials Used in MRT Welding
- Safety Protocols in MRT Welding
- Tools and Equipment for MRT Welding
- Common Challenges in MRT Welding
- Quality Assurance in MRT Welding
- Innovations in MRT Welding
- Career Opportunities in MRT Welding
What is MRT Welding?
Alright, let's start with the basics. MRT welding refers to the process of joining metals specifically for Mass Rapid Transit (MRT) systems. These systems include trains, tracks, and other infrastructure components that require high-strength, durable connections. Unlike regular welding, MRT welding demands precision due to the massive loads and vibrations these structures endure daily.
Think about it – an MRT train can weigh several tons, and it moves at speeds of up to 80 km/h. The welds holding those tracks together need to be flawless. Any weak spot could lead to catastrophic failures. That's why MRT welding is such a critical component of modern transportation infrastructure.
Oh, and before you think this is all about heavy-duty machinery, let me tell you – there's a lot of finesse involved too. Welders working on MRT projects often have to deal with tight spaces, complex geometries, and strict deadlines. It's not just about brute force; it's about skill, knowledge, and experience.
Why is MRT Welding Unique?
Here's the deal – MRT welding stands out from other types of welding because of its specialized requirements. For one, the materials used in MRT systems are often different from those found in regular construction projects. Rail tracks, for example, are typically made from high-carbon steel, which requires specific welding techniques to ensure proper fusion.
Additionally, MRT welding often involves working on-site, sometimes in challenging environments like tunnels or elevated platforms. This adds another layer of complexity to the process. Welders need to be adaptable and resourceful, able to tackle whatever comes their way.
And let's not forget the importance of documentation. Every weld on an MRT project must be meticulously recorded and inspected to ensure compliance with safety standards. This level of detail is crucial when you're dealing with something as important as public transportation.
Importance of MRT Welding
Okay, so you get the gist of what MRT welding is, but why does it matter? Well, here's the thing – without proper welding techniques, MRT systems wouldn't function as smoothly or safely as they do. The importance of MRT welding can't be overstated, especially when you consider the millions of people who rely on these systems every day.
First off, MRT welding ensures the structural integrity of rail systems. Those seamless tracks you see aren't just there for aesthetics. They're designed to minimize vibrations and noise, providing a smoother ride for passengers. And guess what? It's all thanks to skilled welders who know how to create strong, reliable connections.
Then there's the safety factor. MRT systems operate under intense conditions, with heavy loads and high speeds. Any failure in the welds could result in accidents, injuries, or even fatalities. By adhering to strict welding standards, engineers and welders help prevent these kinds of disasters.
Key Benefits of MRT Welding
- Enhanced safety for passengers and workers
- Improved efficiency in train operations
- Reduced maintenance costs over time
- Longer lifespan for infrastructure components
And let's not forget the environmental benefits. By creating more efficient transportation systems, MRT welding contributes to reducing carbon emissions and promoting sustainable urban development. It's a win-win situation for everyone involved.
Types of MRT Welding Techniques
Now that we've established the importance of MRT welding, let's talk about the different techniques used in this field. There are several methods employed depending on the specific application and materials involved. Here's a quick rundown of the most common ones:
Gas Metal Arc Welding (GMAW)
Also known as MIG welding, this technique is widely used in MRT projects due to its versatility and speed. It involves using a continuous wire electrode fed through a welding gun, creating a strong, consistent weld. GMAW is particularly effective for joining thicker metals like those used in rail tracks.
Tungsten Inert Gas Welding (TIG)
TIG welding is ideal for precision work, making it a favorite among welders working on intricate components of MRT systems. This method uses a non-consumable tungsten electrode and an inert gas shield to produce clean, high-quality welds. While it may take longer than GMAW, the results are worth it for critical applications.
Submerged Arc Welding (SAW)
For large-scale projects like laying down miles of rail tracks, submerged arc welding is the go-to technique. It involves burying the arc under a layer of flux, which protects the weld from contamination and reduces spatter. SAW is known for its deep penetration and high deposition rates, making it perfect for heavy-duty MRT construction.
Of course, there are other techniques as well, each with its own set of advantages and limitations. The key is choosing the right method for the job at hand. And that's where experience and expertise come into play.
Materials Used in MRT Welding
When it comes to MRT welding, the choice of materials is crucial. Different components of an MRT system require specific types of metals to ensure optimal performance and longevity. Here's a look at some of the most commonly used materials in this field:
- High-carbon steel for rail tracks
- Stainless steel for structural components
- Aluminum alloys for lightweight applications
Each material has its own unique properties that make it suitable for certain tasks. For instance, high-carbon steel is favored for rail tracks because of its strength and durability. Meanwhile, aluminum alloys are often used for train carriages due to their lightweight nature, which improves fuel efficiency.
It's also worth noting that the welding process can affect the properties of these materials. That's why it's important to select the right welding technique and parameters to avoid compromising the integrity of the weld.
Safety Protocols in MRT Welding
Safety should always be a top priority in any welding project, and MRT welding is no exception. With the potential hazards involved, it's crucial to follow strict safety protocols to protect both workers and the public. Here are some key safety measures to keep in mind:
- Wear appropriate personal protective equipment (PPE), including helmets, gloves, and fire-resistant clothing
- Ensure proper ventilation in confined spaces to prevent exposure to toxic fumes
- Conduct regular inspections of welding equipment to identify and address any issues promptly
And let's not forget the importance of training. Welders working on MRT projects should undergo comprehensive safety training to familiarize themselves with the specific risks involved and how to mitigate them. After all, knowledge is power, and in this case, it can save lives.
Tools and Equipment for MRT Welding
Having the right tools and equipment is essential for successful MRT welding. From welding machines to inspection devices, there's a wide range of gear that welders rely on to get the job done. Here's a look at some of the must-haves:
- Welding machines (GMAW, TIG, SAW, etc.)
- Welding torches and guns
- Ultrasonic testing equipment for quality assurance
Investing in high-quality tools and equipment not only improves productivity but also enhances safety. Plus, it helps ensure that every weld meets the required standards, reducing the need for rework and saving time and money in the long run.
Common Challenges in MRT Welding
Let's face it – MRT welding isn't without its challenges. From environmental factors to technical difficulties, welders often encounter obstacles that require quick thinking and problem-solving skills. Here are some of the most common challenges:
- Working in confined or elevated spaces
- Dealing with extreme weather conditions
- Ensuring uniformity in welds across long distances
Overcoming these challenges requires a combination of experience, adaptability, and teamwork. By anticipating potential issues and planning accordingly, welders can minimize downtime and ensure projects stay on schedule.
Quality Assurance in MRT Welding
Quality assurance is a critical aspect of MRT welding. Every weld must meet stringent standards to ensure the safety and reliability of the MRT system. This involves a combination of visual inspections, non-destructive testing, and destructive testing where necessary.
Some of the most commonly used quality assurance methods include:
- Ultrasonic testing (UT)
- Radiographic testing (RT)
- Magnetic particle inspection (MPI)
These methods help identify defects or inconsistencies in the welds that may not be visible to the naked eye. By catching these issues early, engineers can take corrective action before they become bigger problems.
Innovations in MRT Welding
The field of MRT welding is constantly evolving, with new technologies and techniques emerging all the time. From automation to advanced materials, these innovations are revolutionizing the way we approach MRT projects. Here are a few examples:
- Robotics for precision welding in hard-to-reach areas
- New alloy developments for improved performance
- Smart sensors for real-time monitoring of weld quality
By embracing these innovations, the MRT welding industry can continue to improve efficiency, safety, and sustainability. And who knows? Maybe one day we'll see fully autonomous welding systems capable of handling even the most complex MRT projects.
Career Opportunities in MRT Welding
So, you're interested in pursuing a career in MRT welding? Great choice! With the global demand for public transportation infrastructure on the rise, there's never been a better time to get into this field. Here are some potential career paths to consider:
- Welder technician

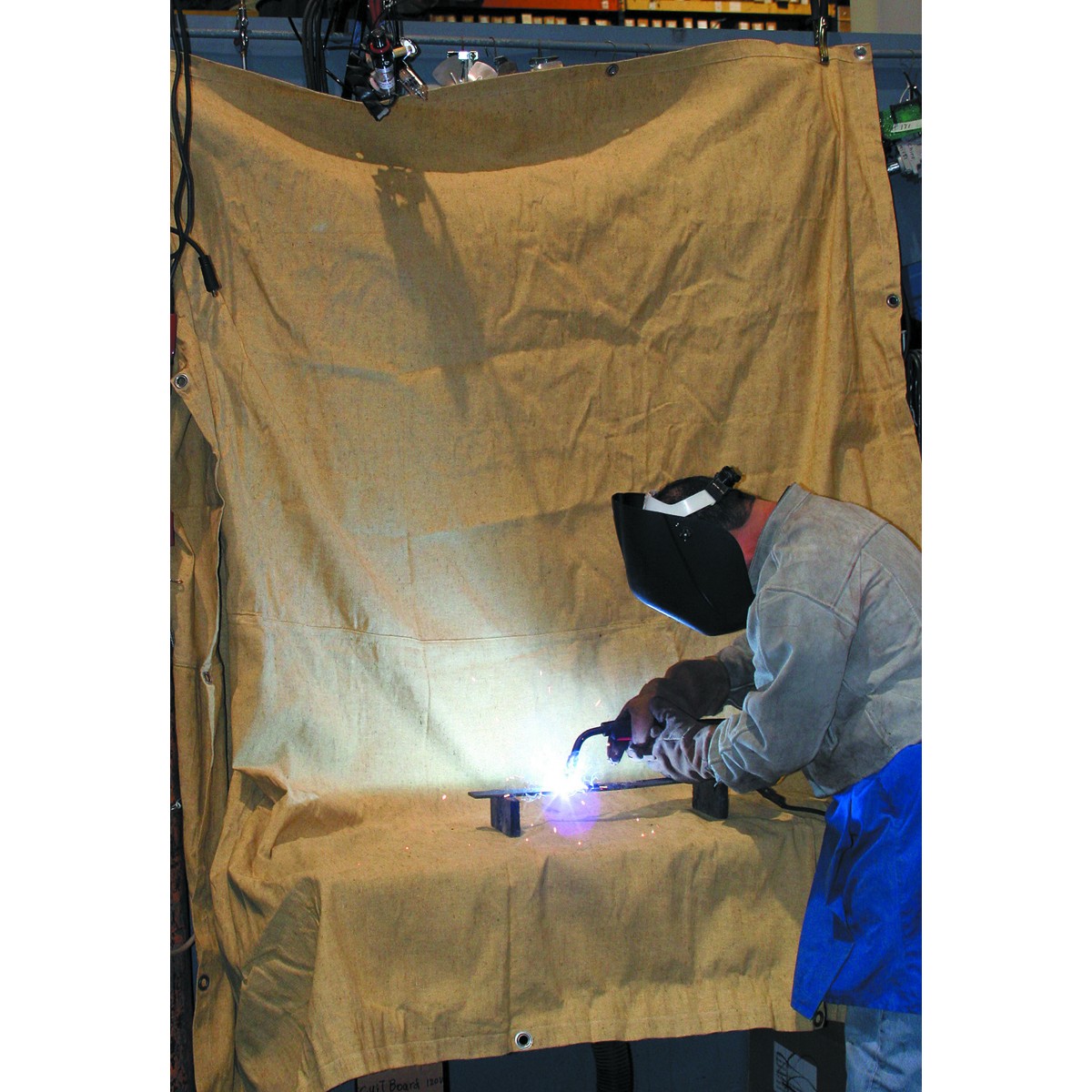
Detail Author:
- Name : Leta Trantow
- Username : fcrona
- Email : hansen.jackson@terry.com
- Birthdate : 1994-12-11
- Address : 70381 Ezra Place Albinaland, RI 32160-9185
- Phone : 520.418.2062
- Company : Leuschke-Hickle
- Job : Pipefitter
- Bio : Hic error vero occaecati rerum. Natus quis quasi deleniti facilis culpa. Quo porro perspiciatis incidunt ut assumenda dolorum voluptatem.
Socials
linkedin:
- url : https://linkedin.com/in/grayson_leffler
- username : grayson_leffler
- bio : Vero perspiciatis ipsam dignissimos cum.
- followers : 2133
- following : 2490
instagram:
- url : https://instagram.com/grayson_official
- username : grayson_official
- bio : Qui maxime laboriosam unde quam. Perferendis fuga est ipsam. Aut quam ea eos laborum nemo.
- followers : 4533
- following : 1481